The Project
The main objective of the NewSOC project is significantly improving performance, durability, and cost competitiveness of solid oxide cells & stacks compared to state-of-the-art. NewSOC targets:
- 25% Increase of the applicable electrolysis current at degradation rates below 1%/1000 h
- 25% Reduction of the area specific resistance
- 25% Increase of cycling stability for reversible operation, thermal and load cycling
- 25% Reduction of cell manufacturing costs, and
- 25% Reduction of toxic organics or materials during manufacture.
The NewSOC project will validate the new cells & stacks at the level of large cells with > 50 cm2 active area and short-stacks in close collaboration with industry.
The NewSOC project will provide a path on how to increase the maturity of the technology from a level where the technology is developed to a level where it is demonstrated. The NewSOC project will evaluate the new Solid Oxide Cell (SOC) materials and fabrication processes with both a life cycle impact and cost assessment including interpretation through the ecoefficiency framework.
Solid oxide electrolysis cells:
First generation of solid oxide fuel cells (SOFCs) have achieved a fairly mature state for highly efficient production of electricity and heat. Apart from this application, solid oxide cells (SOCs) have significant potential for use as electrolysers to efficiently convert electricity into gas/liquids for distribution, storage and later use in the energy sector, transport and chemical industry. SOEC are interesting for large-scale hydrogen production for refinery and chemical industry. In addition, SOCs can balance the fluctuating nature of electricity from renewable sources by changing operation mode reversibly between SOFC and SOEC (rSOC) and by operating dynamically in one of the modes (either SOFC or SOEC). A particularly attractive feature of SOCs is that they can use hydrocarbon fuels for SOFC, and electrolyse steam together with CO2 (co-SOEC). This feature opens the opportunity of directly integrating carbon containing energy sources (such as biogas) and to utilize CO2 efficiently in a closed carbon cycle or even CO2 reduction (e.g. from biogas). Furthermore, SOEC can thus re-use gas emissions in steel mill or cement factories (such as CO generation from CO2 electrolysis or co-SOEC to produce synthesis gas). All these modes of operation of SOC enable integration of larger shares of renewable sources into the energy systems throughout European countries and the world. Competitive SOC technologies in all operating modes (SOFC, SOE, rSOC) need cost competitive, robust and durable next generation SOCs. This is the general objective of the NewSOC project.
NewSOC Concepts and methodology:
Current solid oxide cell (SOC) concepts and versions of them are numerous, both on cell and stack level (fuel electrode supported, metal supported, or monolithic SOC). On the other hand, all SOCs consist of a number of basic building blocks as illustrated in Figure 1, which are often composed of a limited set of materials. Figure 1 also illustrates the concepts currently pursued by the major European industry players in the area. The NewSOC project unites industry players with all the illustrated concepts. The NewSOC project aims at improving performance, durability, and manufacturing costs by improving SoA SOCs on different levels, from components, to cells, and stacks.
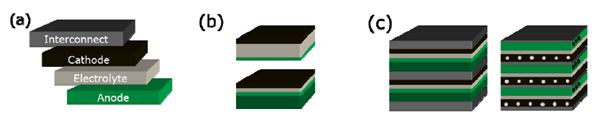
Figure 1: Illustration of (a) generic building blocks for SOC cells & stacks, (b) cell concepts: electrolyte supported, fuel electrode supported & metal supported (from top to bottom b), (c) stack concepts: stacking cells using metallic interconnects & ceramic SOC block (from left to right)
With these concepts, European SOFC technology is at demonstration (for example EU PACE project) and early commercial level (for example BlueGEN from SolidPower) for stationary applications. Solid oxide electrolysis (SOE) technology moves towards demonstration level. Furthermore, the most recent concept - reversible SOCs - is getting more and more attention. The current demonstration and field tests have revealed strengths and challenges, which should not prevent early commercial products. However, industry, with the help of research, needs to overcome these challenges for the achievement of cost competitive commercial SOCs products in a rapidly developing energy technology world where the competition is worldwide. Therefore, the New SOC project develops next generation SOCs. The NewSOC project proposes innovative concepts in the following areas:
- SoA SOCs deliver the expected performances for demonstration and initial markets. Fundamental studies have however revealed that these materials have a large potential for improvement – based on advanced micro structural and computational studies, especially for SOE and rSOC operation more recently addressed than SOFC. The key is structural optimisation and innovative architectures
- Apart from SoA materials, alternative materials have been identified, which allow for overcoming challenges, which are inherent in the currently used materials (e.g. impurity tolerances, redox stability), challenges, that have been identified for example through field testing.
- Upscaling and cost competitive production of SOC technology is a critical parameter. The NewSOC project develops innovative methods of manufacturing with reduction of the needed raw materials and critical raw materials and thus total cost reduction and reduction of environmental footprint, a parameter that has not yet been in the focus.
The NewSOC project will develop and integrate twelve specific concepts (see illustration in Figure 2). They involve a large variety of materials, architectures, and components/interfaces of the SOC stack:
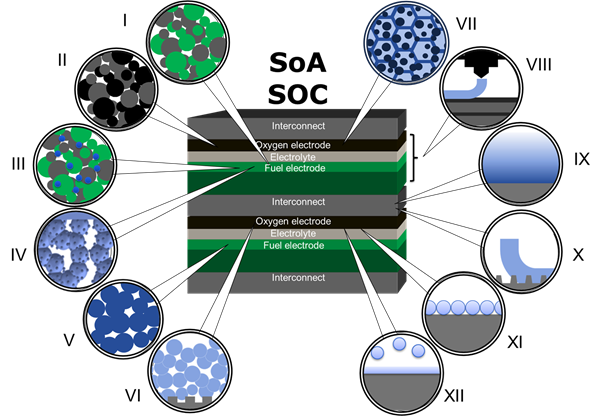
Figure 2: Illustration of the twelve concepts pursued in NewSOC
- Ni based fuel electrode
- LSCF based oxygen electrode
- Bi-metallic or tri-metallic Ni based fuel electrode
- Infiltrated, doped titanate backbone fuel electrode
- Doped lanthanum chromite based fuel electrode
- Patterned electrode/electrolyte interface for Co-free oxygen electrode
- Honeycomb supported oxygen electrode
- 3D printing of SOC
- Protective coating through inkjet printing
- Ceramic coatings with innovative interface concepts
- Thin film atomic layer deposition barrier layers
- Thin film room temperature sputtering barrier layer
All concepts proposing new materials in the NewSOC project have proven to achieve at least 70% key performances as compared to SoA, as required in the call.